Optimierung des Ersatzteil-Lagers bei einem Automotive-Zulieferer
Lager-Layout | Lager-Organisation | Pick-Raten
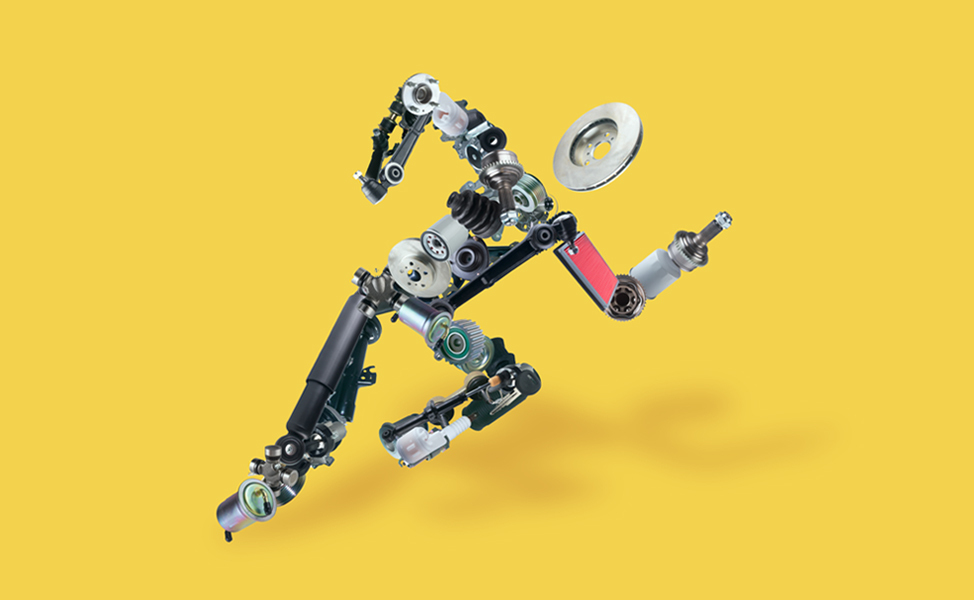
Das Projekt in Stichworten:
- Analyse der Prozesse identifiziert Lager-Layout als zentrale Schwäche
- Lager-Layout nach ABC-Analyse an den Auftragseingang angepasst
- Mehr Festanstellungen verringern Fluktuation und Krankenstand deutlich
- Auftragsrückstand um 90 Prozent reduziert
- Liefertreue für täglichen Neueingang erreicht
Der Interim-Manager wurde von der Ersatzteilsparte (IAM) eines Automobil-Zulieferers damit betraut, als Supply Chain Improvement Manager den weltweit größten Lagerstandort zu reorganisieren. Das 20.000 qm große Lager (250 Mitarbeitende, 15.000 Artikel) verzeichnete zu diesem Zeitpunkt regelmäßige Auftragsrückstände von ungefähr zehn Tagen. Der Interim Manager sollte den Standort führen, die hohen Auftragsrückstände schnellstens reduzieren und mit einem Personalkonzept die hohe Mitarbeiter-Fluktuation sowie den hohen Krankenstand nachhaltig zu senken.
Analyse der Prozesse identifiziert Lager-Layout als zentrale Schwäche
Um die Gründe für die Auftragsrückstände zu ermitteln, analysierte der Interim Manager zunächst die die Kennzahlen. Zudem machte er sich in vielen „Walk the process“-Rundgängen ein eigenes Bild und führte zahlreiche Gespräche mit Mitarbeitenden. Dabei stellte sich schnell heraus: Die Lagerorganisation entsprach nicht den Anforderungen der sich stetig verändernden Auftragsstrukturen. Die Ware war an vielen Stellen im Lager schlicht am falschen Platz - mit zu langen Wegen und einem unklaren Nachschubprozess. Hinzu kam die Schwierigkeit, dass die rund 15.000 SKU in den einzelnen Lagerbereichen (automatisiertes Hochregal, manuelles Hochregal, Blocklager und automatisiertes Kleinteilelager) nicht nach den Pickfrequenzen gelagert wurden. Außerdem berücksichtigten die Pick-Aufträge die großen Gewichtsunterschiede der Produkte nur unzureichend. Erschwerend kam hinzu, dass die Staplerflotte überaltert war und hohe Ausfallzeiten durch Reparaturen aufwies.
Lager-Layout nach ABC-Analyse an den Auftragseingang angepasst
Mit diesen ersten Erkenntnissen erarbeitete der Interim-Manager gemeinsam mit dem Management und leitenden Mitarbeitenden einen Plan für eine neue Lagerorganisation und ein neues Lagerlayout. Im Anschluss an eine ABC-Analyse begann die Umorganisation: Schnelldreher bekamen fixe Plätze mit kurzen Wegen zugeordnet und Langsamdreher längere Wege mit teilweise variabler Platzzuordnung. Das automatisierte Hochregal sorgte nur noch für den Nachschub. Damit wurde sichergestellt, dass Anbruchpaletten nicht wieder zurück ins Hochregal gelangten. Das stabilisierte die Leistungsfähigkeit des Hochregals.
Um die Verfügbarkeit der A-Artikel jederzeit zu gewährleisten, entwickelte der Interim Manager in Anlehnung an Lean-Methoden eine Systematik, die den Nachschub im gesamten Lager optimierte. Der räumliche Tausch von Warenein- und -ausgang ermöglichte, dass der Warenfluss deutlich besser lief.
Mehr Festanstellungen verringern Fluktuation und Krankenstand deutlich
In enger Abstimmung mit dem Betriebsrat und der HR-Abteilung entwickelte der Interim Manager im nächsten Schritt ein Personalkonzept, um Fluktuation und Krankenstand zu senken. Im Ergebnis wandelte das Unternehmen eine hohe Zahl an Arbeitnehmerüberlassungsverträgen (ANÜ) in Fest-Anstellungen um. Zu Beginn des Mandats betrug das Verhältnis von 70/30 zugunsten von ANÜ – nun beträgt es 65/35 für Festanstellungsverträge. Durch Wertschätzung und die Aussicht auf einen Festvertrag sank der Krankenstand von 10 auf 4 Prozent. Außerdem stieg die Motivation der Mitarbeitenden, zur Abarbeitung des Auftragsrückstandes Sonderschichten einzulegen, die – in enger Abstimmung mit dem lokalen Betriebsrat - auch an Wochenenden stattfanden.
Auftragsrückstand um 90 Prozent reduziert | Liefertreue für täglichen Neueingang
Nach vier Monaten Vorbereitungs- und Umstellungszeit trugen die Maßnahmen erste Früchte. Mit Inbetriebnahme der neuen Struktur schafften die Mitarbeitenden in der ersten Woche 13.000 Picks. Nach Feinjustierungen der Prozesse stieg die Quote auf eine dauerhafte Leistung von 14.000 Picks/Tag – nach durchschnittlich 11.500 Picks vor Mandatsbeginn.
In Kombination mit Sonderschichten reduzierten sich die Auftragsrückstände in den folgenden Monaten von zehn Tagen auf einen Tag - bei gleichzeitiger Liefertreue des täglichen Auftragseingangs. Mit der Umstellung auf Festverträge stieg die Motivation der Mitarbeitenden merkbar an und führte auch dauerhaft zu einem branchenüblichen Krankenstand.
Für den überalterten Flurförderzeug-Fuhrpark erstellte der Interim Manager eine Ausschreibung, die zu 25 Prozent Einsparung beim Kauf der Maschinen führte.
Am Ende des 9-monatigen Projektes konnte der heutige Interim Manager das Lager in sehr gutem Zustand an den neuen Verantwortlichen übergeben.
Buchen Sie jetzt online einen Gesprächstermin mit einem Consultant Ihrer Wahl.
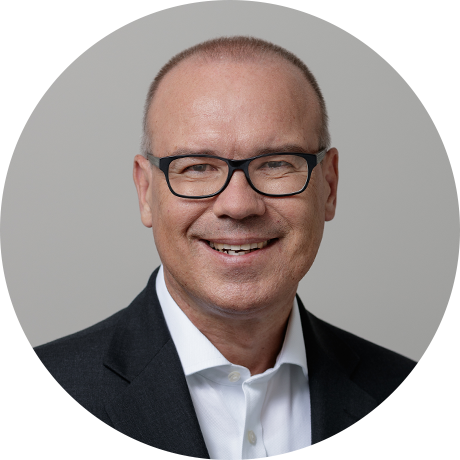
Christoph Domhardt
Senior Consultant | Prokurist
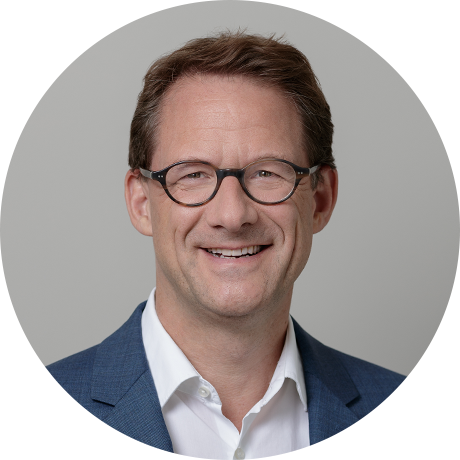
Tilo Ferrari
CEO
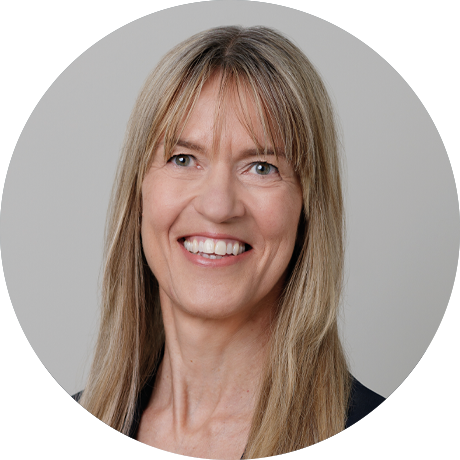